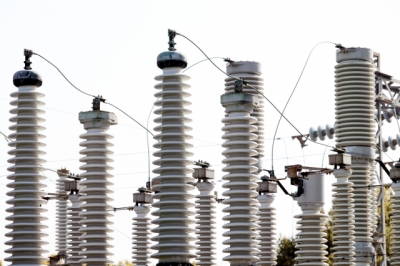
前号ではセラミックス製造の混錬を記載しましたが、今回は成形工程以降です。
【成形工程】
成形方法には押出し、射出成形、加圧成形、鋳込み等がある。
押出し成形はセラミックス原料である粘度に圧力をかけ口金(一種の金型)から押出す方式。断面積が一定なのでパイプ状に適しており自動車排ガス用フィルターなどの多孔質セラミックス製造に適している。
押出し速度を一定にしないと断面積形状が変化してしまい、他に粘土成分、密度、特性も一定にする必要あり。
生産性向上を狙い押出し速度を高めると圧力による摩擦熱で原料特性が変化したり、口金の摩耗が激しくなる。かといって水分量を増やすと強度不足で重力に負け押出し直後に成形体として形状を維持できなくなり、可能な限り小さな力で押し出せる流動性と口金を出た時に形が崩れない保形成が必要である。
鋳込み成形とはセラミックス原料に水を入れてスラリーを作り、型に流し込む方式。
但しセラミックスは吸水量に限界があり厚手の製品が作れず、粒子の密度分布が広がってしまうため乾燥・焼成工程で変形が起こりやすい。最近では温度や化学変化を利用してスラリーを型内で固化させるゲルギャスト法が開発され、複雑な形状を簡単に成形することが出来るようになりつつある。
このように成形工程も進歩を遂げているものの、ベースとなるスラリーの粒度配合、水素イオン濃度の調整、分散剤添加で濃度、粘性、粒子凝集状態の徹底管理を行っている。
【焼成工程】(日本ガイシ技術資料より)
セラミックス成形体に熱を与えることで水分、バインダーを除去することで原料粒子同士が密着し、粒子間距離が縮小することで全体が縮小する。
この現象を焼結と呼び、焼成温度が高いほど、原料粒子が小さく・丸く・粒子分布が揃っているほど焼結後の製品は緻密になり硬くなる。
焼成工程で硬度・強度以外にも気孔率、電磁気的、熱的特性が決まる。焼成時間・温度・雰囲気など条件を変えることでいろいろな機能が作り出せる。
セラミックスの焼成では時間をかけながら温度を上昇させ、最高温度を保持したあと常温に戻す工程が一般的だ。ゆっくりと温度を上昇させる初期の領域では混練時に加えた水分やバインダーを熱で除去することで、原料粒子間の距離が縮み成形品全体が縮小する。急激に温度を上昇させると成形体の表面と内部に温度差や収縮差が生じてしまうため、クラックなどの原因となる。
次の領域では初期の領域から高温とすることで原料粒子が結合し更に収縮する。
温度上昇時間、ピーク温度及び維持時間によって製品の機能(気孔率、耐熱性、教祖)が決定されるため、非常に重要な領域であり各企業のノウハウである。
ピーク後の冷却領域では原料によっては収縮するケースもあるので、沈降温度と時間の管理が必要。
焼成釜は主に2種類。
一つはある大きさの釜を用意し成形体を投入し、上述のAからC工程の順に焼き上げる方法のバッチ処理だ。
もう一つは流し焚きの方法を用いるトンネル釜方式。高さ2~3メートル、長さ数十メートル以上の煉瓦造りのトンネルを作り、その中をトロッコ列車(の様な)が走行する。トロッコ列車の荷台にセラミックス成形体を並べてお
き、例えば午前9時に1番トロッコを出発させ、2番トロッコは昼の12時に出発させるといった具合に間隔をあけて投入し、予熱帯、焼成帯、冷却帯を通過させて行く。
1928年に日本ガイシが流し焚きを開始し、焼成帯でバーナー加熱するときに発生した燃焼ガスを予熱帯に流し、成形体加熱後の釜出口で排気する方法を採用してきたが、ピーク温度領域で発生した燃焼ガスの熱量によって予熱帯での温度が決まってしまうため釜内部の温度差が発生し易く、狙った温度分布を実現するためにはファインセラミックス製品のより高度化から温度管理が難しくなり、従来の流し焚きでは焼成が難しくなり、2001年からは新しい焼成方法に変更されている。
バーナー内部に蓄熱体を装備したリジェネバーナーの採用で、燃焼と排気を周期的に切り替えることで蓄熱体を介して燃焼ガスの熱を回収し、燃焼空気を予熱するもの。
またゾーン制御と呼ぶAからC領域にで各々発生した燃焼ガスを各領域で排気することで各領域での独立した温度制御を組み合わせている。
このリジェネバーナーとゾーン制御によりトンネル釜の温度コントロール性は飛躍的に向上し、焼成品質、焼成時間、効率とも大幅に向上した。
但し、これでも排気として熱が捨てられているため、これを熱源として利用することが研究・開発されている。
これとは別に投入されるエネルギー量を減少させる方式も考えられている。
セラミックス焼成を低温で行いたいという願いはオイルショック以降、高まった。低温焼成はエネルギーコスト低減に直結するが、及び釜構成部品の損傷低減や安価な材料活用が見込める。
低温焼成のためには焼結助剤添加、加圧焼結、易焼結粉末の利用などがある。
焼結助剤添加によりセラミックス原料原子の拡散や焼結速度の上昇が見込めるが、添加剤により製品の高温特性の低下が若干見られ、この犠牲を余儀なくされても構わない場合に用いられている。
加圧効果はホロプレス方式があり、高温・高圧力を利用する。
排ガスフィルターメーカーの実際の製造ラインでは焼成前に100度強の熱風乾燥で水分をある程度飛ばしているのは日本の2大メーカーとも当時同様であった。
焼成工程では製品投入後の最高温度は一般的にコージェライトでは1,000+数百度で焼き上げるが、最高温度到達を急ぐとクラックが発生するためゆっくりと温度を上昇させて行く。ところが到達までの時間が競合に比べ早いのが日本ガイシさん。さすがです。
【加工工程】
ファインセラミックスは一般に難加工である。
しかし焼成を終えた段階では表面状態など出荷出来る状態になく、要求通りの形状・特性に合わせた仕上げが必要だ。
その一つがダイヤモンド等の砥粒を使った研削で砥石の粒子や削る時の荷重加減が材料によって決定される。ナノオーダーのものではレーザーによる熱源や化学エネルギーを利用するケースも。
[多孔質ファインセラミックスについて](国立科学博物館産業技術史より)
多孔質セラミックスは多数の細孔と耐熱性、強度、耐食性を併せ持ち、分離、吸着、ろ過、拡散などのフィルター、触媒担体、吸着材、断熱材、吸音対など広い用途がある。
細孔は20Å以下のミクロポア、20~500Åのメソポア、500Å以上のマクロポアに分類される。
他に開気孔と閉気孔にも大別され貫通もしくは非貫通の開気孔、閉気孔など。開気孔は主に分級やろ過に、閉気孔は断熱や吸音に利用される。
細孔は原料粒子相互に形成される空隙に由来するマクロポアとゼオライトに見られる粒子内のミクロポア、中間のメソポアに分かれる。
一般に焼成工程で存在するのはマクロポアであり、自動車排ガスフィルターのハニカムでは薄壁中の細孔をミクロポアとして、薄壁によって形成されるチャンネルをマクロポアとする二様性細孔構造。
排ガスフィルターとしての用途では補足される環境汚染物質の粒子径は最大細孔径によって決まる。
細孔径分布は焼結体の特性としてある細孔径でピークとなり、一様性の細孔構造となるが、原料骨材(粒子)の粒子分布を均一化すると細孔径分布はシャープになる。ミクロポアを持つ粒子を適正な条件で製造すると細孔径分布は大小2つのピークを持ち二様性を持つ。触媒担体として用いるときはミクロ・マクロポアの2つが共存するように細孔径分布を制御する場合も。
また触媒担体として用いる場合には単位重量当たりの物質の表面積(比表面積)が重要となり、ガス圧力の変化に対してのガス成分の吸着量の変化を調べ、吸着量を求める。比表面積を大きくとるために平均細孔径の微細化と細孔容積の増加が必要。
次回は自動車の排ガス規制。
(山田順一)
(情報提供を目的にしており内容を保証したわけではありません。投資に関しては御自身の責任と判断で願います。また、当該情報は執筆時点での取材及び調査に基づいております。配信時点と状況が変化している可能性があります。)