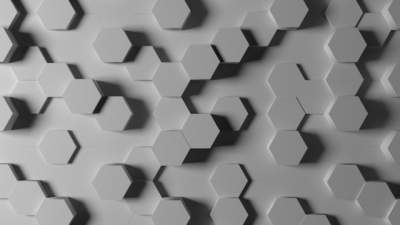
自動車触媒担持用ハニカムフィルター(ガソリンエンジン用)のプレーヤーは日本ガイシとコーニングが2強で各々50%弱のシェア。残りはトヨタグループのデンソーで、素材の異なるメタルハニカムでは新日鉄住金マテリアルズ(日鉄ケミカル&マテリアル)。
触媒コンバータで初期に採用されたセラミックス材料はコージェライトが選定され現在でも利用されている。コージェライトはアルミナ、タルク、カオリンなど土中に含まれる成分でコストは・・・安いですね。
酸化アルミニウム(通称アルミナ)は地球上で酸素、珪素に次ぎ多い元素で、硝酸アルミニウムや硫酸アルミニウムを1200~1300度Cで熱分解または塩化アルミニウムを酸素または水蒸気で1000度C以上で反応させる。
酸化アルミニウムの2019年の輸入価格はキロ当たり30.9円。
カオリンはカオリン石から取れる粘土鉱物の一種で、カオリンの含有率が高いほど高温に耐える磁器となる。アルミ、シリコン、酸素からなり価格はトン当たり5万円台で、タルクも同様の価格帯でキロ換算だと数十円程度になり
ましょう。
この3つの粉末を混錬する際、水分やつなぎが必要となるが素早く混ぜようとすると料理でいうところの“ダマ”が出来てしまう。
まずは粉末だけを混合し、次に水を加えて混練して行くが、短時間で効率良く混ぜる工夫がされている。
エレクトロニクス向けなど小さく機能性が要求される製品のセラミックスでは分散剤を液体に混ぜて紛体に馴染むようにし、分散剤に覆われることにより粉末は再凝集させない効果もある。
粉末、水、バインダー、その他原料を混ぜて作ったスラリーは、粉末粒子の周りに空気が存在しない塊でなければならない。
粉末(粘土)粒子の隙間に水が入り込んで潤滑油のような役目をして、滑りや水と密着して粘りを出して原料粒子を引き付け合わせるという練る工程が重要。時間をかけて練ると滑りやすさを出るが乾燥後に割れてしまうことから、製品の特性に合わせて小さい力、大きい力など機械を使い分けて練りの工程を行う。
練りでは成型時に形を変えやすいほどの柔らかさ、成型後にはその形を維持できるほどの硬さの粘土にしている。
10割蕎麦ではポロポロと途切れてしまい裏テクニックがあるとかで、セラミックスの世界でも増粘剤やら混ぜてと裏方企業の存在もありましょう。
DPFも含め裏方の中小企業名が特許に出てきます。
[ハニカム製造に於ける歴史]
昭和40年代
排ガス規制強化からハニカム型とペレット型の2つが候補となる。
ハニカムは軽量で背圧が低いものの高コストに対して、ペレット型は担体が粒状で破壊の心配ないが、背圧・重量が重い。
昭和46年(1971)
日本ガイシがハニカムの研究開始。他に世界で20社がハニカムの研究を始める。
昭和47年
日本ガイシが押し出しでのハニカム製造に成功するが国内自動車メーカーは評価せず。
米国GMはペレット型採用方針で日本ガイシ製を評価せず、唯一フォードのみがハニカムを採用の方針。
昭和48・49年
日本ガイシが試作品を米触媒メーカーであるエンゲルハルトに提供するも熱衝撃性弱くクラック入り改良に入る。そして衝撃性改良品をフォード、エンゲル社に提供。この頃に米コーニング社のハニカムが評価される。
昭和50年
日本ガイシにフォードからハニカム100万個の価格と納期照会。フォードはハニカム使用の方針を決める。この時点でハニカム開発企業は米国勢3社と日本ガイシ、デンソーの合計5社に減少。
GMはペレット型を採用決定。理由はハニカムの低信頼性と供給企業の少なさ。
昭和50年11月
日本ガイシ、フォードから150万個の引き合いが来る。
12月にサンプルテスト不合格、契約交渉中断。低熱膨張品の開発急務。
昭和51年
1月 日本ガイシが低熱膨張品開発し、フォードのテスト合格。
3月 月産3万個の量産ライン完成。
10月 フォードへ2万個出荷。
昭和52年
フォードから薄壁化(300→150ミクロン)要求。
月産12万個体制
日系自動車メーカーもハニカム方式に採用にシフト。
昭和53年
日本ガイシ 薄壁化完成
ハニカムは自動車走行中に於ける急激な温度変化や3次元の大きな振動、そして耐熱性といった厳しい要求から、低膨張かつ耐熱性の材料が検討された。
全てのセラミックス材料で1,000度C以上の使用環境に耐えられるが、
膨張係数の大きさでアルミナとムライトは除外された。
リチウム・アルミニウム・シリケート及びアルニウム・チタネートの熱膨張係数は低いものの高コストであり、後者は高温で熱分解することで対象外となり、コージェライトが選ばれた。
コージェライト結晶は熱膨張性に異方性があるのが特徴で、この特徴を活かして低膨張化を実現している。A軸、B軸、C軸の結晶軸は各々熱膨張率が異なり、特にC軸方向ではマイナスの膨張係数をとることが特徴的である。
含有率が高いほど耐熱性が上昇するカオリンのカオリナイト結晶は板状の平たい結晶構造であることから、圧力をかけて口金を通す成形過程でせん断力を受けて結晶の方向がハニカムセル面と同じ方向に配向する。この現象があったからこそコージェライトの低膨張ハニカムが完成した訳だ。
ところが、このメカニズムは当初わからなかった。
低膨張材料の開発実験中に焼成後のコージェライト原料粉末を粉砕した時に、ある条件のもとで結晶方向が揃う現象を日本ガイシの技術者が発見したのだ。
コージェライト結晶はカオリナイト結晶を基準に生成するため、負の膨張性を示すC軸方向がハニカムの壁面と平行となって成長する。
このためハニカム構造体の熱膨張に寄与しないセル壁厚み方向に高膨張成分が向けられ、低膨張率のハニカム構造体が完成した。
日本ガイシは日米欧で特許を申請したが、コーニングが先に低熱膨張コージェライトとして特許を出願していたため、長い交渉ののち昭和53年にクロスライセンスとして技術提携し、コーニング社と対等合弁で販売企業エヌコアを設立した経緯がある。
現在ではセラミックス製触媒単体(ハニカム)供給企業は世界3社でシェア100%であり、新規参入はほぼ不可能。
上述した原料を分級したのち混練りし押し出し口金を通すが、日本ガイシでは独自方法であったが1976年に英国企業とクロスライセンス契約を結び特許問題を解決。
だが口金(金型)の製造が難しい。
口金裏側から入った粘土スラリーは口金内部のスリットを通過する際に十文字に広がり、隣通しのスラリーが圧着・合体してハニカムを形成する。この口金内部のスリット加工には放電加工が施され、それ以外にもドリルなどが用いられている。
ドリル加工する穴の深さと径の比、つまりアスペクト比は20を超え、穴の数も数千となるため非常に難しい金型製造となる。口金はハニカムの直径より多少大きい程度であり大きさは10センチ強と小さいが、価格は驚くほど高い。
比較対象にするべきかの問題はあるが、重量当たり単価では超高級車ブカッティ・ヴェイロンと比べて桁違い。
ここにも裏方企業が登場する。
金属中に緩やかながらも曲がった穴を形成可能とする凄腕企業が存在し、モノを見させて頂いてビックリ。三菱重工、ブリジストンなどメジャー企業の裏方として活躍している。
排ガス規制がより厳しくなる先進国では薄壁2ミルの方に、新興国でも一部の国ではより薄壁化へ、新興国では搭載無しから搭載の方向へ向いて行くことが予想される。
現在、コージェライトハニカムの競合品はメタル製しかなく、日鉄グループが製造販売を行っているものの、高価で採用が増えている状況になさそう(数年前の段階)。
約20年前だが、スバルのスポーツ車両であるインプレッサWRXはターボ搭載のハイパワーエンジンでメタル製の触媒担体を使用していた。エンジンルーム内での取り回し(配置)からコージェライト製は無理で、形体を変更できるメタル製でしか解決出来なかったからであるとの回答をスバル技術者から得ている。300万円を超える価格帯であるから採用できたとの側面もあろう。
コージェライトハニカムが登場して40年以上。これを代替するものは未だ出てこない。
(イノベーションリサーチ 山田順一)
(情報提供を目的にしており内容を保証したわけではありません。投資に関しては御自身の責任と判断で願います。また、当該情報は執筆時点での取材及び調査に基づいております。配信時点と状況が変化している可能性があります。)